洗浄・研磨のプロセス
洗浄
研磨する前に、鉄研では独自の洗浄方法「クリーンバレル」によって製品についた油を除去します。
研磨
製品ごとにメディア(研磨に使用する砥石)を職人が組み合わせ、バレル(研削・研磨)を行います。
油を除去する
プレス加工時に製品に必要となる油。しかし、汚れた油を完全に除去しないまま研磨することが
実は不良の原因となることがあります。表面状態をよりクリーンにしてからバレルをする。そんな非常識が、鉄研が辿り着いた常識でした。
従来工法
0.4μの世界
プレス機によって高い圧力で型抜きされた製品の表面を0.4μ(*1ミクロン = 1/1000ミリ)の世界まで拡大すると、製品の表面には加工油と製品から出たコンタミンがついています。
さらに、プレス時の高い圧力により発熱し、コンタミンの混ざった加工油が焼き付き、固着しています。
油(炭化水素系)で洗浄し、研磨
従来の炭化水素系洗浄を行うと、
加工油と沈んでいたコンタミンはとれるが、
固着層は残り、新たに炭化水素の油膜もできる。※ アルカリ系洗浄でも、油膜は残らないものの、固着層は残るため結果は同じである。
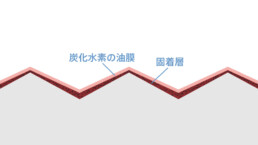
この状態で洗剤の中で研磨すると、
研磨により製品とともに固着層も削られ、
加工油とコンタミンが分離し、細かい粒子になる。
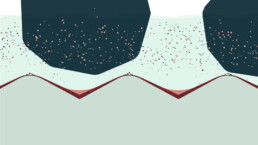
細かくなった加工油と炭化水素が
酸化により粘着性の物質に変化する。
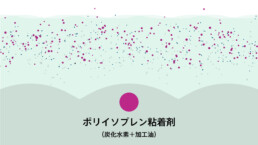
ほかの粒子や洗剤が
粘着性物質により吸着されて、
製品の表面に1つの層となって残ってしまう。
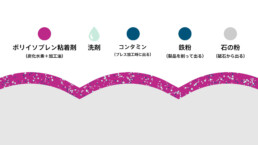
従来工法による洗浄後の断面観測
高性能集束イオンビーム装置(FIB)を使用したイオンビームによる微細部の加工・観察結果(観察倍率:90,000倍)
炭化水素洗浄の場合、
0.3~0.05μの炭化水素の硬質皮膜(ハイドロカーボン)
を形成することを観測。
つまり
従来の洗浄では、製品の表面は汚れたまま
=油がついている状態
であることがわかる。
この状態でいくら
研磨を行っても最終的には表面に
汚れが残り、不良の原因
となります。
そこで
クリーンバレル洗浄
Clean Barrel
クリーンバレル
After Clean Barrel
クリーンバレル後の分析結果
断面観察
油の剥離除去
鉄研では、固着層を煮沸することで油をゲル状に戻し、さらに超音波を当てることで剥離除去を可能にしている。90,000倍で撮影しても顕著な異物は確認されない。(油分ゼロ)
クリーンバレルによる洗浄後の断面観測
高性能集束イオンビーム装置(FIB)を使用したイオンビームによる微細部の加工・観察結果(観察倍率:90,000倍)
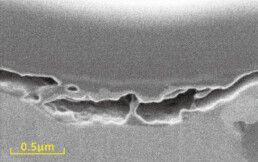
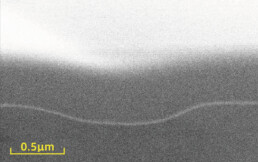
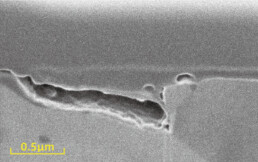
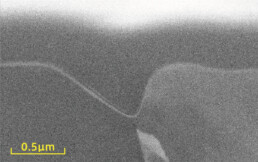
成分分析
表面の炭素が減少
炭化水素系洗浄被膜は、通常の脱脂液では分解できないので、製品表面にシミが発生した場合は酸処理を施さなければ除去できないが、炭化水素系硬質皮膜(ハイドロカーボン)や油の劣化(酸化・水酸化)により生成されるポリイソプレン粘着剤(生ゴム)を、剥離除去出来るカーボンリンス洗浄の配合に成功。
参考)シミの濃淡は、油膜の厚み(0.4μ)により可視化するのでBofore(左)の表面画像の白い部分にも炭化水素系硬質皮膜(ハイドロカーボン)は存在している。
表面画像の比較
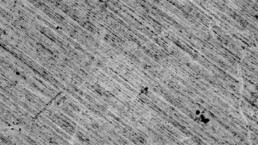
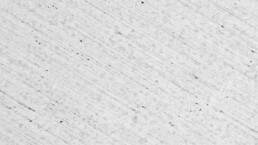
分析装置:6010LA 加速電圧:5.00kV プロセスタイム:T3 ライブタイム:50.00秒 リアルタイム:55.94秒 デッドタイム:11.00% カウントレート:13154.00CPS
表面の侵食率
侵食なし
炭化水素系皮膜《ハイドロカーボン(炭化水素系硬質皮膜)、ポリイソプレン粘着剤(生ゴム)》は、酸性の処理を施すと除去する事が可能だが酸によって金属表面まで侵食される事で肌が荒れ白くなり易い。カーボンリンス洗浄では、表面状態をほとんど変える事無く油膜の完全除去が可能。
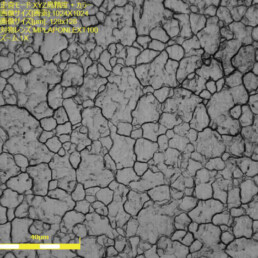
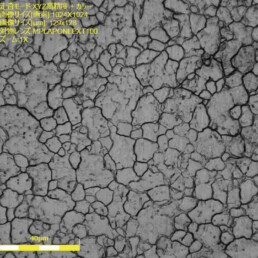
評価領域:129µm × 128µm フィルタ:ガウシアンフィルタ 対物レンズ:x100
面粗さ
表面状態を正確に計測可能
従来の油系洗浄(炭化水素系洗浄など)では表面に皮膜を形成するため、実際の表面状態を観察測定する事が出来なかったので、二次加工上(熱処理・研磨・メッキ・塗装・防錆等・・)の様々な不具合の起因を発見する事が困難だった。3D測定レーザー顕微鏡にて検査測定してみても、ハイドロカーボン(炭化水素系硬質皮膜)の表面を測定してしまい、製品本来の表面状態が計測出来ない。しかし、クリーンバレル洗浄を行った製品では、製品表面に被膜がないため、正確な表面状態を観察することが可能となる。